
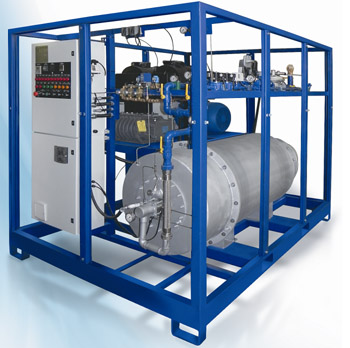
Промышленный парогенератор
"ИНТЕРБЛОК"
Модернизация паросилового хозяйства
предприятий стройиндустрии России
Как известно, тепловлажностная обработка бетонных и железобетонных изделий является важнейшей частью технологического процесса производства ЖБИ на предприятиях стройиндустрии. Затраты на производство пара для ТВО могут достигать 80-90% от общих затрат предприятия на тепловую энергию. Постоянно растущие цены на энергоносители приводят к росту стоимости производства тепловой энергии. Дополнительное увеличение стоимости теплоносителя приносит эксплуатация устаревших паропроизводящих котельных, паровые котлы которых, в силу конструктивных и эксплуатационных особенностей, не могут эффективно регулировать подачу пара в зависимости от потребностей завода. Производитель сборного железобетона вынужден принимать пар на свою производственную площадку даже при отсутствии в нём необходимости. В этих случаях пар просто выбрасывается в атмосферу.
Энергетический анализ паросилового хозяйства некоторых заводов ЖБИ, выполненный специалистами инженерной компании ИНТЕРБЛОК, выявил значительный перерасход тепловой энергии при производстве бетонных и железобетонных изделий.
Основными причинами завышенного потребления тепловой энергии являются устаревшие нормативы, которыми до настоящего времени пользуются предприятия ЖБИ при расчетах количества тепловой энергии на 1 м3 железобетонных изделий, необходимой для их тепловой обработки, а также несовершенные устаревшие паровые котлы и другое теплоэнергетическое оборудование. В результате только один завод ЖБИ средней производительности бесполезно выбрасывает в атмосферу до 30 млн. рублей в год.
В настоящее время предприятия используют «Временные нормы для расчета расхода тепловой энергии при тепловлажностной обработке сборных бетонных и железобетонных изделий в заводских условиях» СН 513-79, разработанные в 1966 г. и переизданные в 1979 г. Этот документ декларирует использование (и соответственно оплату) теплоносителя (пара или нагретой воды) круглогодично, независимо от потребностей, включая выходные дни, время на проведение профилактических работ, отсутствие изделий в пропарочных камерах и т.п. В соответствии с указанными документом нормативный расход пара на тепловлажностную обработку 1 м3 железобетонных изделий определяется в 0,2 – 0,4 Гкал. Средний расход тепла на предприятиях страны по стране составляет 0,36 Гкал на 1 м3.
Реальная потребность железобетонных производств в тепловой энергии, рассчитанная специалистами инженерной компании ИНТЕРБЛОК, в 8-10 раз меньше.
В целях снижения затрат на производство тепла для ТВО некоторые предприятия применяют установки, в которых теплоносителем являются нагретый воздух или продукты сгорания жидкого или газообразного углеводородного топлива, т.н. «турбогаз». Применение горячего воздуха или «турбогаза» приводит к интенсивному испарению влаги из бетона, отрицательно сказывается на полноте гидратации и процессах структурообразования в цементном камне, расположенном в поверхностном слое бетона, снижению прочностных характеристик железобетонных изделий. Возникает опасность попадания продуктов сгорания в производственный цех, что может создать опасность для здоровья людей. Применение подобных установок для ТВО недопустимо.
В настоящее время, для тепловлажностной обработки ЖБИ наибольшее распространение в России и за рубежом получила технология производства парогазовоздушной смеси – технологического пара, на основе применения промышленных парогенераторов "ИнтерБлок". Опыт их эксплуатации на заводах ЖБИ, КПД и др. показал, что данная технология позволяет сократить расходы на производство пара при изготовлении железобетона на 50-70%, а в некоторых случаях – в несколько раз.
Например, на одном из заводов Калужской области потребление тепла в сутки при непрерывной работе централизованной котельной составляло 31,2 Гкал. При стоимости 1 Гкал тепла 1800 руб., затраты на тепловую энергию составляли 56160 руб./сутки. Переход к децентрализованному теплоснабжению с применением промышленного парогенератора "ИнтерБлок" (для ТВО, прогрева инертных материалов) позволило экономить 16,5 млн. руб в год.
На заводе ЖБИ в Челябинской области переход от собственной централизованной котельной к полному автономному теплоснабжению на базе парогенераторов "ИнтерБлок" привел к сокращению расхода топлива (природного газа) до 600 тыс. куб.м. в месяц. Экономия составила 30 млн. руб в год.
Преимуществами парогенераторов "ИнтерБлок" являются:
– высокая экономичность – тепловой КПД 99%,
– время включения и выключения – 15 секунд,
– универсальность – один парогенератор производит как технологический пар, так и нагретую воду для технологических и бытовых нужд,
– низкое давление технологического пара на выходе – не более 0,06 МПа,
– диапазон рабочих температур пара 110-180 °С,
– температура нагретой воды до 90 °С,
– парогенератор не требует дымовых труб,
– нет необходимости в сложных системах водоподготовки и деаэрации, используются простые системы умягчения воды,
– парогенераторы не требуют строительства фундаментов и могут устанавливаться в цеху в непосредственной близости от пропарочных камер,
– применяемые виды топлива – природный газ, пропан или дизельное топливо.
В течение многих лет эксплуатации парогенераторы серии ST успешно зарекомендовали себя на предприятиях России, Украины, Белоруссии, Казахстана, Великобритании, Канады, Китая, Норвегии, Польши, США, Южной Кореи.
Технические характеристики промышленных парогенераторов "ИнтерБлок"
ПОКАЗАТЕЛЬ | ST-102H | ST-302H | ST-502H | ST-1002H |
Тепловая мощность, кВт | 290 | 870 | 1450 | 2900 |
Тепловая мощность, Гкал/час | 0,25 | 0,75 | 1,25 | 2,5 |
Эквивалентная паропроизводительность, т/час | 0,5 | 1,5 | 2,5 | 5,0 |
Диапазон рабочих температур пара, °C | 100–160 | 100–160 | 100–160 | 100–160 |
Температура нагретой воды, °C | 80 | 80 | 80 | 80 |
КПД, % | 99 | 99 | 99 | 99 |
Давление пара, МПа | ≤0,05 | ≤0,05 | ≤0,05 | ≤0,05 |
Потребляемая электрическая мощность, кВт | 5,5 | 15 | 35 | 56 |
Максимальный расход воды, л/мин (м3/час) | 4 (2,4) | 12 (7,2) | 19 (11,4) | 38 (22,8) |
Максимальный расход природного газа, м3/час | 28 | 85 | 142 | 284 |
Максимальный расход пропана, л/час | 34 | 100 | 170 | 332 |
Максимальный расход дизельного топлива, л/час | 23 | 69 | 115 | 230 |
Вес установки, т | 1,7 | 2,2 | 3,8 | 5,2 |
Размеры: – длина (м) | 1,8 | 2,0 | 2,3 | 2,6 |
– ширина (м) | 1,4 | 1,7 | 1,9 | 2,2 |
– высота (м) | 1,6 | 1,8 | 2,0 | 2,3 |
Рассмотрим технологический процесс тепловлажностной обработки железобетонных и бетонных изделий с использованием парогенератора "ИнтерБлок", представленный на рис. 1.
Изделия в камерах выдерживаются в течение 2 часов (зона А). В это время за счет экзотермического процесса гидратации цемента температура в камерах поднимается до 30-35 °С. После процесса выдержки парогенератор включается на максимальный режим, и температура в камерах поднимается со скоростью 17-20 °С/час. Подъем температуры осуществляется в течение 3 часов (зона Б) до заданной температуры 60-70 °С, после чего парогенератор переходит на минимальный режим работы и необходимая температура в камерах поддерживается в течение 6 часов (зона В). Затем парогенератор выключается, и изделия остывают в течение 3-4 часов (зона Г).
Цикл набора прочности бетонных изделий в пропарочных камерах, согласно технологическому регламенту, длится 12–13 часов, из которых парогенератор работает в максимальном режиме в течение 2,5–3 часов, а в режиме минимального потребления топлива 5–6 часов.
В настоящее время парогенераторы "ИнтерБлок" являются одними из самых надежных и экономичных в своем классе оборудования, что обеспечивает существенное снижение себестоимости выпускаемой продукции и небольшой срок окупаемости оборудования.
В целях модернизации паросилового хозяйства заводов ЖБИ, КПД, ДСК и других предприятий стройиндустрии, ООО Инженерная компания ИНТЕРБЛОК выполняет работы по созданию автономных теплоэнергетических систем, замене устаревшего теплоэнергетического оборудования на современные промышленные парогенераторы "ИнтерБлок", а также автоматизацию технологических процессов тепловлажностной обработки бетонных и железобетонных изделий.
Генеральный директор
Инженерной компании ИНТЕРБЛОК
Богомолов О.В.
Москва, ул. Кулакова, 20, стр. 1Б, комн. 22. Тел.: (495) 722-72-86, 728-92-93.
|
Старый Оскол, ул. Прядченко, 118, офис 36. Тел./факс: (4725) 42-79-01.